Our main products: Amino silicone, block silicone, hydrophilic silicone,all of their silicone emulsion,wetting rubbing fastness improver, water repellent(Fluorine free,Carbon 6,Carbon 8), demin washing chemicals(ABS, Enzyme, Spandex protector, Manganese remover), Main export countries: India, Pakistan, Bangladesh, Türkiye, Indonesia, Uzbekistan, etc.,more detail please contact : Mandy +86 19856618619 (Whatsapp )
★Silicon softener
Natural fibers such as cotton, linen, wool, silk, etc., after bleaching, dyeing, printing processing or functional finishing, the removal of wax and oil stains causes certain damage to the fibers, resulting in rougher fabrics, darker luster, and even affecting sewing performance. Therefore, soft finishing is necessary. The hand feel of synthetic fibers is inferior to that of natural fibers such as cotton, wool, silk, and hemp. After high-temperature shaping, synthetic fiber fabrics become very rough and hard in hand feel. Only through soft finishing can the natural fibers be endowed with a soft hand feel to improve their performance.
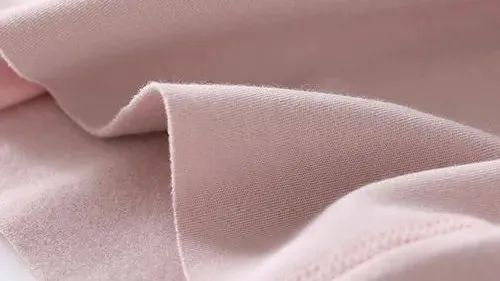
Silicon softener can give fabrics a soft, smooth, full and elastic feel, as well as anti wrinkle, wear-resistant, water-resistant and good sewing properties, which greatly improves the added value of the product and is therefore favored by customers; However, defects such as silicone oil spots often occur during the soft finishing process, which can cause great trouble for dyeing and finishing processes.
①Characteristics of Silicone Softener
The suitable working conditions and physicochemical characteristics of silicone softeners can be summarized into the following three points:
1. The pH value of the work bath is relatively stable between 5 and 6.5;
2. The most suitable temperature for work baths is 30-45 ℃;
3. Ionic, most varieties are cationic, followed by non-ionic; There are a few varieties that are anionic (comparing the softness effects of various varieties, cationic varieties generally dominate).
②Development stages and characteristics of Silicone softeners
The development stages of silicone softeners can be roughly divided into four generations.
The first generation: dimethyl silicone oil and hydroxyl modified silicone oil. Characteristics: low cost, not washable, easy to break emulsion.
Second generation: Epoxy modified silicone softener, amino modified silicone softener Characteristics: Non hydrophilic, easy to break emulsion, epoxy modified focuses on dryness, amino modified focuses on smoothness, amino modified silicone oil has yellowing problems
Third generation: Polyether modified silicone softener. Characteristics: Good hydrophilicity, not easy to break emulsion, but poor hand feel
Fourth generation: Linear block copolymer modified organic silicone softener features: good hydrophilicity, soft hand feel, low yellowing, and not easy to break emulsion
③Common problems and solutions during application
Ⅰ、The influence of pH value on silicone oil
The stability of softeners is sensitive to pH value. In the general dyeing and finishing process, cotton fabrics need to undergo pre-treatment, which usually involves the use of alkali or alkaline substances to remove impurities from the fabric. Some fabrics also need to undergo silk finishing, and the alkali used in these processes is difficult to clean inside the fibers. Alkali is also used for dyeing with reactive or vat dyes, so the fabric surface may become alkaline during post finishing.
Ordinary silicone oil is generally not alkali resistant and is prone to breaking under alkaline conditions. After a period of time during immersion rolling and softening processing, it will stick to the rollers, resulting in silicone oil spots.
★ Solution
Before soft processing, the fabric surface must be washed with alkali agent.
2. Add acetic acid to the working fluid and maintain the pH of the rolling groove at 5-6.
Ⅱ、 The influence of fixed locomotive speed factors
When producing ultra-thin fabrics such as chiffon, imitation silk, and bari yarn, the speed of the dyeing factory setting machine is very fast, sometimes reaching 60-80 meters per minute. However, due to the low liquid content of thin fabrics, poor permeability of the fabric itself, and poor hydrophilicity of silicone oil, ordinary silicone oil has poor shear resistance, and the silicone oil liquid brought up by the fabric will flow back on the rolling mill, which can easily cause roller sticking.
★ Solution
1. Try to control the speed of the vehicle as much as possible.
2. Improve the permeability of the fabric surface.
3. When using, pay attention to replacing the groove working fluid and regularly cleaning the rollers.
Ⅲ、 Problems that are prone to occur with softener on the cylinder
In order to achieve a certain tactile style and meet the actual production needs of the factory, some factories often need to perform immersion softening finishing in the cylinder. However, due to structural factors and residual substances in the dye vat, some silicone oils and mixtures may stick to the cylinder wall. Over time, some black oily viscous substances will form on the cylinder wall, which will form silicone oil spots on the fabric surface.
★ Solution:
1. Strengthen cleaning work.
2. Try to choose silicone oil with good stability in the cylinder.
3.Before applying silicone oil in the cylinder, the cloth surface should be cleaned and free from alkali; Add some acid appropriately and adjust the pH value to around 6.
Post time: Jan-14-2025